Furnace Brazing
Common Applications:
- Hydraulic Fittings
- Heat Exchangers
- Tube Manipulations
- Machined & Pressed Assemblies
- Automotive Components
- Medical, Scientific and General Engineering Components
Brazing has often been overlooked by designers, possibly due to a poor historical image. The modern brazing process and materials are a far cry from this perception however - it has become an exceptional joining process that makes possible engineering assemblies with joint strengths that cannot be achieved by any other means.
Contact: Chris Marsh on 0121 567 3218, Mobile: 07747 446 763, Email: [Javascript protected email address]
Vacuum Furnace Brazing
Vacuum brazing offers flux free joints of the highest integrity, strength and cleanliness.
Vacuum brazing is used for joining a wide range of alloys and complex shapes & sizes and can often incorporate a subsequent heat treatment process. Vacuum brazing also offers the widest choice of brazing alloys and properties.
Vacuum brazing offers slow heating and cooling rates which can reduce internal stresses, which in turn can give improved thermal and mechanical properties of the materials being brazed.
- Working zone of 1200 x 1200 x 1200
- Maximum operating temperature of 1400ºC
- Maximum gross load of 1500kg
- Can operate with a partial pressure of Nitrogen, Argon or Hydrogen
- Gas quench option
- Meets the requirements of AMS-2750 Version E
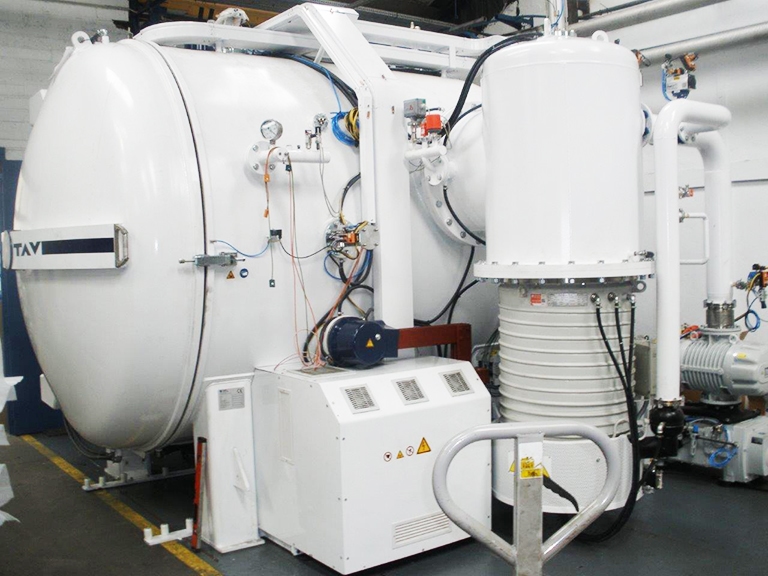
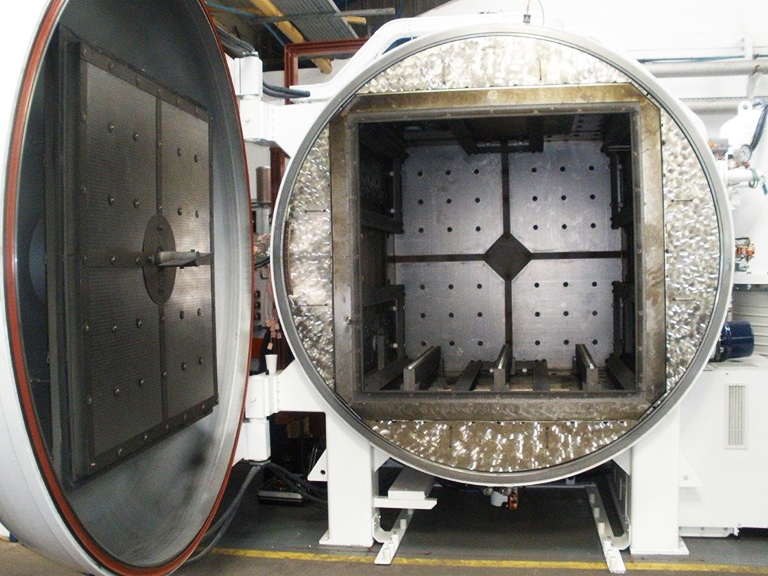
Vacuum Brazing is commonly used by the following market sectors:
- Aerospace
- Defence
- Heat Exchangers
- Marine
- Medical
- Motorsport, including F1
- Power generation / Nuclear
- Scientific
Mesh Belt Brazing
Often referred to as Bright Brazing, Copper Brazing, Continuous Brazing, Atmosphere Brazing. An ideal process for very low to very high volume parts in steel or stainless steel. Carried out under a reducing furnace atmosphere resulting in a clean component & one requiring no post braze cleaning.
Hydrogen Brazing
Hydrogen Brazing uses the strongly reducing characteristics of hydrogen to clean/reduce the oxides that are usually present on the mating surfaces of most materials being brazed. This in turn aids the wetting/bonding of the brazing alloy being used which can increase the strength of the brazed joint. Hydrogen Brazing (especially in a humpback furnace) gives exceptional results on most stainless steels but it cannot be used for brazing titanium alloys.
The benefits of Hydrogen Brazing include:
- Cleanliness - Hydrogen Brazing reduces surface oxides on the parent material which improves the cleanliness and integrity of the brazed joint.
- Flexibility - Hydrogen Brazing increases the braze alloy material options - i.e. it enables the use of high vapour pressure braze alloys that cannot be brazed in a vacuum atmosphere.
- Material Choice - Hydrogen Brazing can be applied to a multitude of materials such as stainless steel, copper and certain nickel based alloys.
Hydrogen Brazing can give exceptional brazing results when carried out using a humpback furnace. A flow of pure dry hydrogen continually refreshes the furnace atmosphere which helps to reduce surface oxides & other possible contamination on the assemblies to be hydrogen brazed. This in turn improves the wetting characteristics of the braze alloys.
Typical Applications
Furnace Brazing is still one of the least appreciated manufacturing techniques with many engineers being unaware of its existence or its advantages as a method of joining two or more parts together.
Kepston use furnace atmospheres that permit the brazing of multi-jointed components in mild steel and/or Stainless Steel without the use of flux.
Typical Applications
The list of potential applications is substantial, however, the most common categories are:
- Hydraulic Fittings
- Heat Exchangers
- Tube Manipulations
- Machined Assemblies
- Pressed Assemblies
- Fabrications
- Wire Formed Assemblies
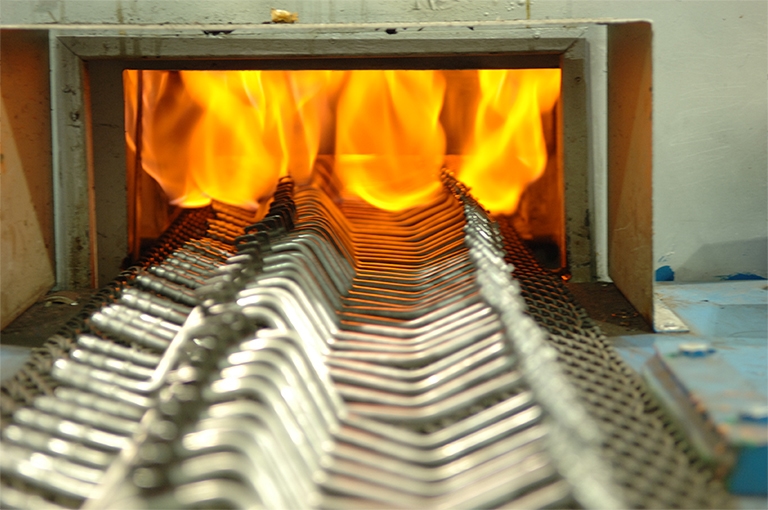
Joint Design
Brazing relies on capillary attraction. Therefore, the joint design is crucial in the success of the brazing. An unbroken capillary path with gaps not exceeding 0.1mm are required for most applications.
Whenever possible, joints should be self-supporting or self-jigging as furnace jigs can be expensive, they may move in the heat during the process and they occupy furnace space adding to the unit costs.
Joint Strength
A correctly designed and brazed joint should produce a strength of joint that is in excess of the parent metal.
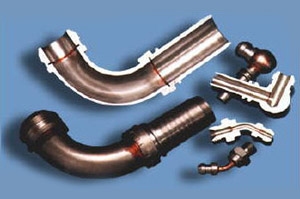
Furnace Brazing Is Also Commonly Referred To As...
Copper Brazing, Bright Brazing, Mesh Belt Brazing & Atmosphere Brazing.
Advantages & Disadvantages
Surface Condition
Components should be clean, free from swarf, rust and excess grease before brazing.
It should be noted that score marks, shot blasted or roughened areas in the region of the brazed joint will pull the braze filler metal away from the joint.
Post Braze Processes.
Due to the high melting point of the braze material [1083ºC for Copper] most commonly used hardening and case hardening heat treatments can be carried out after brazing. Also most plating processes take well on copper brazed components.
Main Advantages of Furnace Brazing:
- A uniformed heating & cooling rate can reduce the potential for distortion.
- Joint strengths greater than the parent metal are possible.
- Parent metals are not fused or damaged.
- Stresses are relieved during brazing.
- No surface deterioration takes place during the process.
- Dissimilar metals can be brazed together.
- Different metal thickness are permissible in brazed joints.
- Multiple joints can be brazed at once.
- Long and inaccessible joints can be filled successfully.
- Furnace brazing facilitates the manufacture of complex & delicate assemblies which might be impossible to achieve by any other method
- Skilled labour is not required to carry out the process.
- Rapid reproducible results are obtainable.
Disadvantages of Furnace Brazing:
- Close fits are necessary to facilitate the capillary action.
- Component parts will be annealed during the process.
- Provision for location of the brazing material has to be allowed for in the design.
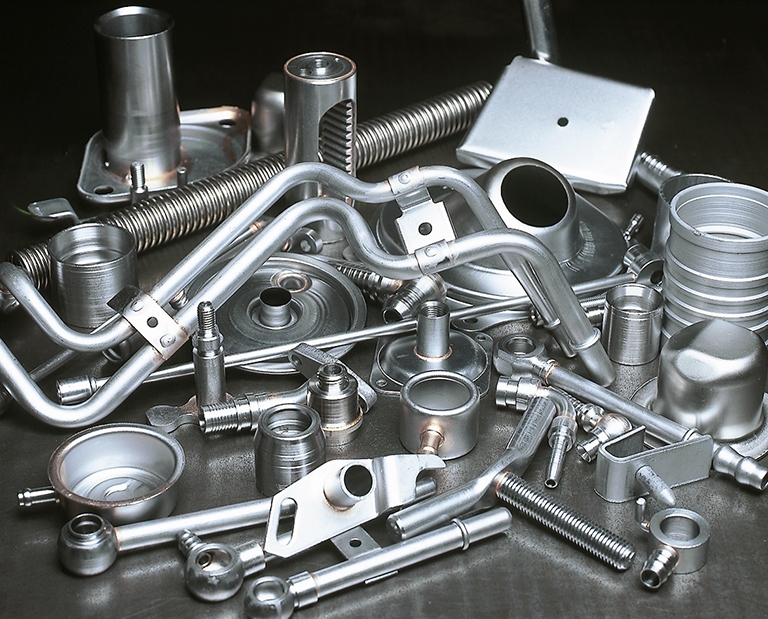